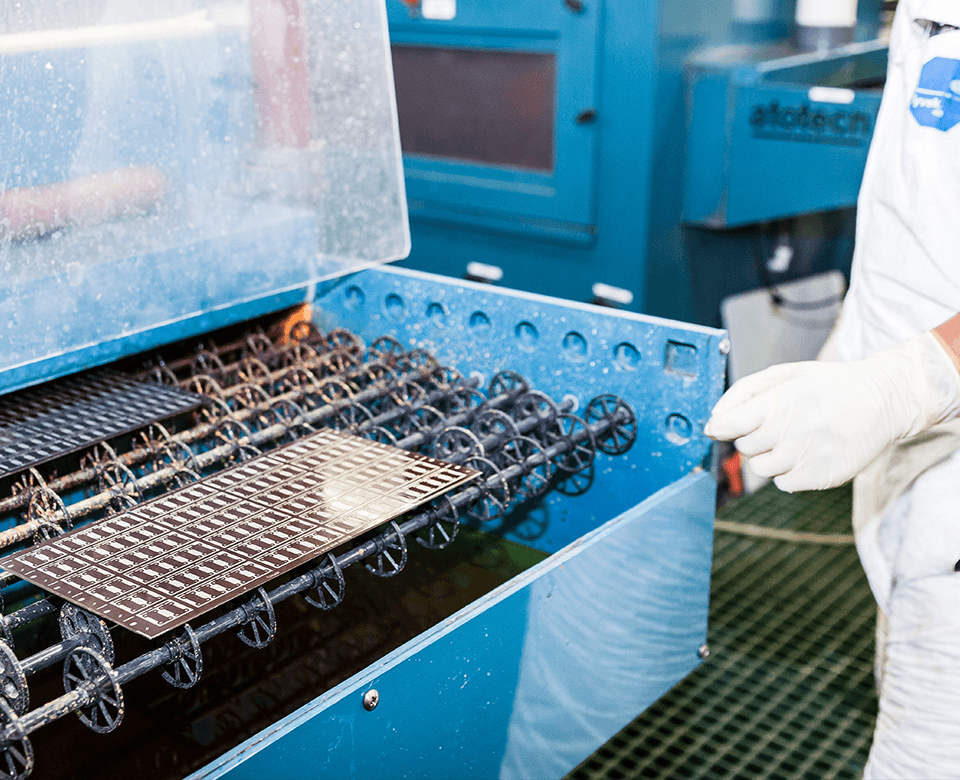
What is Photochemical Machining?
Known by many names, the photochemical machining process, a key aspect of chemical machining services, uses a photosensitive polymer called photoresist to produce a highly precise mask that protects the sheet from the etchant. In Elcon’s process, our team of engineers digitally image the desired pattern onto the photoresist-coated substrate using solid-state UV LEDs. The unexposed resist is removed, leaving just the mask pattern. The sheet is then passed through an etcher which sprays the metal sheet with etchant from both sides. The etchant selectively removes the unmasked metal, precisely machining the features of the part. The mask is then stripped from the metal, resulting in a burr and stress free sheet of precision parts. Our tight process controls offer the ability to achieve tolerances as tight as ±0.0005 in.
With this process, part complexity does not lead to an increase in part cost, giving you the flexibility to produce highly intricate configurations reliably and cost-effectively. Changes to designs are easily adjusted with digital imaging, making our photochemical machining process ideal for prototyping. However, the flexibility, repeatability, and precision of the process also ideally suit it for medium- and high-volume production.
Benefits

- Competitive cost
- Fast turnaround
- Burr-free, stress-free parts
- Low cost tooling
- Metallurgical properties preserved
- Design flexibility
- Wide range of materials
- Dimensional repeatability
- Precise and complex geometries
Capabilities

- Material thickness: 0.0005 in. to 0.100 in., depending on the features. Contact us with any questions!
- Step etching
- Half etching
- 3D photoetching
- Knife and needle edges
- Selective plating
- Typical minimum hole diameter: 1.2x material thickness
- Typical minimum feature spacing: 1.2x material thickness
- See our Design Guidelines for more detail.
Specifications
View applications for photochemical machining, the equipment we use, alternative naming conventions, and more below.